楊宏智教授
1.雷射掃描系統與動態聚焦系統之整合設計[學生丁建芳]
近年來,隨著雷射的蓬勃發展,廣泛地應用於生醫、電子光電、光通訊、量測技術等用途,可針對材料進行切割、鑽孔、焊接、雕刻、表面處理等製程。在雷射加工系統中,常使用振鏡掃描技術來進行圖案加工,因其擁有快速且精準定位的掃描特性,再搭配不同雷射源,可以提升製程速度與靈活性。而在雷射加工過程中,雷射光束多採用高斯振福分布的型態(TEM00),因其有較高的能量密度,此位置為雷射光束之焦點,亦即整體雷射加工系統之工作距離(working
distance)。若在加工過程中,雷射光束的焦點位置不在表面上,將無法行加工或者加工效果不如預期,因此要如何掌握雷射焦點的位置技術顯得非常重要。
本論文針對雷射光束之焦點位置控制作探討,設計動態聚焦系統於振鏡掃描系統前,透過改變系統內鏡子間之相對位置,來實現對雷射光束之焦點位置控制,即成為可變焦的雷射加工系統,並於變焦範圍內加工具有高度差的工件或圖案。本論文首先利用ZEMAX光學系統設計模擬軟體分析動態聚焦系統內鏡子之配置,不同的配置將對於整體光路系統之成像品質造成影響,同時找出鏡子間相對位置與工作距離的關係,並建立一套光學元件挑選準則(criterion),讓使用者能夠知道光學元件之間的搭配將對於雷射加工系統的影響,最後於實驗中進行驗證。
本論文發現,在動態聚焦系統中之鏡組為"平凹平凸"配置時,系統之成像品質較佳,而設計之動態聚焦系統,其變焦範圍可達25
mm。在變焦的過程中,成像品質會隨著鏡子間的相對位置而改變,發現在"平凹雙凸"配置時成像品質變化較小。再者,由雷射加工實驗中透過觀察工件之熱影響區(Heat
Affect Zone)來評估系統之成像品質,發現成像品質較佳的配置,有較小且均勻的熱影響區。此外,對於本論文設計的動態聚焦系統之變焦能力測試,則透過加工45度斜面來驗證焦點位置的控制,在同樣加工高度差為25
mm之線段時,發現未使用動態聚焦系統之焦點位置控制時,其加工能力不如預期且加工線段只有一小段,理論加工長度與實際加工長度之誤差高達93
%;而有使用動態聚焦系統之焦點位置控制時,理論加工長度與實際加工長度之誤差約為3.2%左右,故可顯示本論文之動態聚焦系統能夠對於雷射光束之焦點控制作控制。
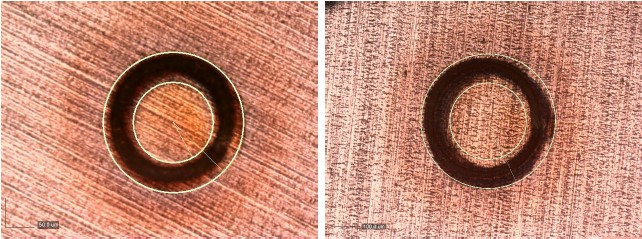
平凹平凸(PLCC-PLCX)配置(左)與平凹雙凸(PLCC-BICX)配置(右)之加工結果
2.工具機主軸製程管制系統與損壞辨識系統開發[學生林威延]
為了提升全球競爭力,提昇產品品質、降低生產成本、縮短製造及維修時間為目前工具機產業必須採取的競爭策略,機械在運作時會產生震動與噪音,並且可以透過監測此數值達到非破壞檢測與監控。但往往受限於成本或無適當量測工具,只能採取試誤法為檢測的方式,不僅浪費時間、材料及人力成本,更降低生產力。本研究透過人工製作以及退修主軸蒐集等兩種方式,建立主軸常見的損壞模型,除了傳統的傅立葉轉換之外,使用了經驗模態分解法和多尺度熵等三種訊號處理方法,開發特徵擷取以及比對演算法,建立主軸損壞辨識系統。由於機械震動通常為非穩態且非線性的訊號,傳統傅立葉轉換有其限制,本研究利用經驗模態分解法將原始訊號拆解成各個內部模態函數,並透過過零點速度以及能量分佈來表示各種模型的訊號特徵,對於大部分的模型分析有顯著效果,且研究中發現,若是為合格主軸,會產生四個目標內部模態函數;若是為組裝瑕疵主軸,例如不對心、潤滑油過多過少、預壓過大過小,會產生五個目標內部模態函數;若是是結構損壞主軸,會產生六個目標內部模態函數;多尺度熵則是計算訊號在各尺度下的亂度值,此方法亦在此研究中驗證針對某些特徵模型有非常佳的辨識效果。
本研究於最後提出快速軟體開發方法,並且利用此方式開發製程管制系統 (Manufacturing Execution System, MES),製程管制系統是指生產現場電子化與製程之控管,系統以即時的方式,收集生產製程中各種資訊,供生產與管理者等參考,除了幫助生產管理者,管控生產製程外,更重要的是透過統計分析,找出每一種主軸最佳的精度參數,搭配本研究開發的損壞辨識系統,於台中工具機廠商驗證,提升其主軸品質。
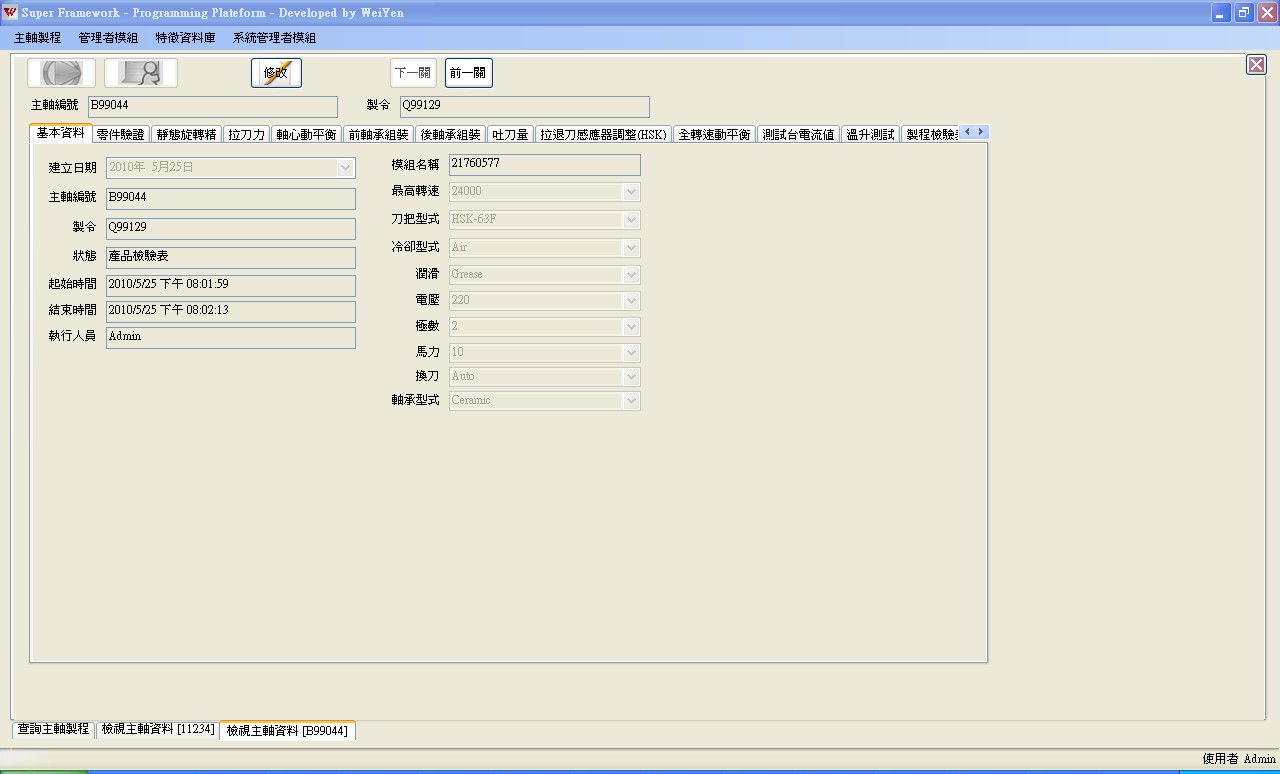
本研究軟體系統架構
主軸履歷維護畫面
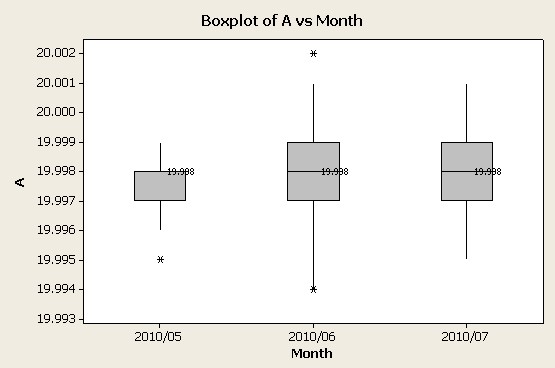
零件公差六個標準差統計報表
3.機械式巡航系統於手術訓練之應用研究[學生陳鼎元]
現今的臨床手術中,許多手術仍僅憑著醫師經驗動刀,伴隨著高風險與不確定性,本研究擬開發出一套機械式巡航系統輔助手術,為醫師規劃出準確的
位置開刀,提升手術的安全性與便捷性。
談到提升精準度與安全性,醫學影像導航手術 (Image-Guided Surgery)
的普及帶來了許多貢獻,臨床上對於避免術後併發症、縮短病患術後復原時間的需求也逐漸增加。
因此,一套精準、靈巧、好用的醫學影像導航系統在這全新世代中,已成為醫師不可或缺的得力助手,縱觀機械式、光學式、電磁式三種醫學影像導航系統,機械式手術導航系統擁有構造簡單、架設方便、行動限制小、應用靈活等優點,使用前不需費時進行繁瑣的設定,也不會產生醫師進行手術時遮蔽光線而失去追蹤的問題,諸多面向,機械式導航系統相較於其它兩者,有著明顯
的優勢。
而本研究先針對治療水腦症病患的腦室穿刺引流手術進行規劃,透過機械手臂搭配CT斷層掃描的資訊,準確地指出最適合穿刺的位置,協助醫師迅速且準確地完成手術,同時擬將這套系統搭配上自製頭形假體,提供新進實習醫師一個精準方便的穿刺練習系統。
利用工業級機械手臂搭配雷射測距儀組合成定位器,輔以3D Slicer三維影像重建軟體、Matlab
GUI圖形化人機介面進行數學演算、座標疊合與訊息傳遞,為醫師做好整組手術的臨床規劃,並經過多次實驗交叉驗證其精準度,以期將此
系統盡快推上臨床使用,為腦室疾病病患謀福祉。
3D Slicer於規劃中介面總覽
面罩型定位器規劃實驗場景
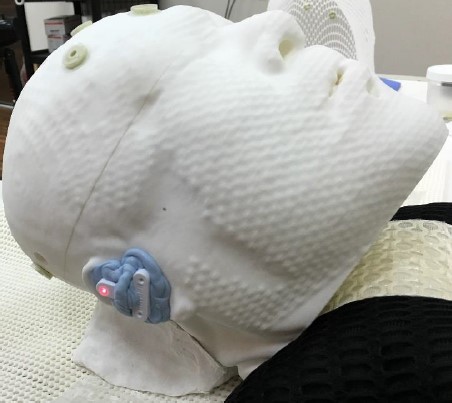
耳戴型定位器規劃實驗 – 雷測儀取點示意圖
4.開創性矽晶穿孔製程導入晶圓級發光二極體封裝基板之研究[學生唐肇蔚]
矽晶穿孔(TSV)製程為三維積體電路、系統級封裝、晶圓級封裝(WLP)等三維堆疊封裝科技之核心關鍵技術,近年來採用矽晶穿孔技術進行三維堆疊封裝儼然已成為封裝業者發展之主要趨勢。探索技術現況,深反應性離子蝕刻(DRIE)製程小從數微米直至數百微米以上尺寸之矽晶穿孔製作皆能勝任,是目前最廣為半導體業者所採用之矽晶穿孔製程方法。然而,深反應性離子蝕刻製程設備相當昂貴,無形中限制了此蝕刻工藝之應用層面。本論文有兩大研究重點,首先係創新矽晶穿孔製程之研發;接續為創新矽晶穿孔製程導入發光二極體封裝基板(LEDsub-mount)應用之分析與驗證。本研究使用灰關聯田口(Grey-Taguchi)方法尋找濕式蝕刻製程之多品質最佳參數,藉由最佳化蝕刻製程移除奈秒雷射製程產生之矽晶缺陷。應用上針對發光二極體封裝基板之散熱性能、基板絕緣電性、高溫可靠度等關鍵特性進行分析與探討。實驗結果顯示灰關聯田口方法可確實找到區域多重品質最佳化參數並有效移除雷射加工產生之矽晶缺陷;採用矽晶穿孔基板作為發光二極體封裝基板能得到較氧化鋁基板優異之散熱性能;創新矽晶穿孔製程導入發光二極體封裝基板應用相較於採奈秒雷射製程能提昇
623
%之崩潰電壓;晶圓級發光二極體封裝基板具備優異之高溫可靠度特性。本文提出之創新矽晶穿孔製程具備有,較低加工成本、高加工效率、優異加工品質等適合半導體相關業者將製程導入量產之關鍵特性。而晶圓級發光二極體封裝基板之關鍵特性與可靠度結果闡述了晶圓級發光二極體封裝基板取代陶瓷封裝基板之潛在機會。
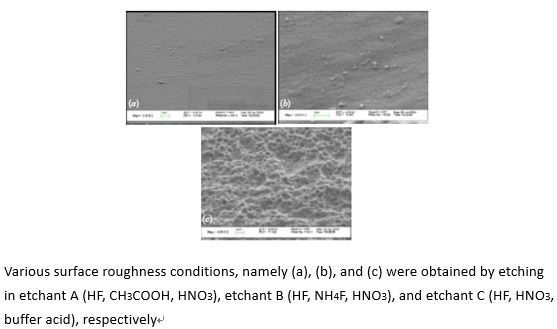
5.矽導通孔製程工程特性之研究[學生洪梓閔]
因應市場對電子產品輕薄之需求,半導體產業不斷地快速發展。為解決目前二維製程微縮上所遇到的困難,讓摩爾定律(Moore’s
Law)能夠延續,應用矽導通孔(TSV)連接之三維積體電路(3D
IC)構裝技術成為產業積極發展的重要技術-其關鍵便在於矽導通孔製程。其中,若一開始的鑽孔製程品質不良,便會對後續製程品質造成影響,進而導致整體成本提升。是故本論文提出在矽深蝕刻完成鑽孔後,進行金屬化製程前,導入業界成熟的濕蝕刻製程,調整製程參數,以提升矽導通孔品質,並透過電子顯微鏡實際觀察與量測其電性進行濕蝕刻效果
之驗證。
根據實驗結果,鑽孔後若利用濕蝕刻,則能清除矽深蝕刻造成的波浪狀側壁,成功得到平滑側壁,並在後續物理氣相沉積製程中,使金屬層覆蓋率獲得顯著提升。對於孔徑
80um
經過濕蝕刻處理後的孔洞,其填銅比例也相對較高。而在電性方面,經過濕蝕刻處理的矽導通孔除表現較佳,量測結果之電阻值與漏電流亦相對較低。總結,本研究開發出業界可用的濕蝕刻製程,有效提升孔洞品質,並確認矽導通孔電性能有所提升。
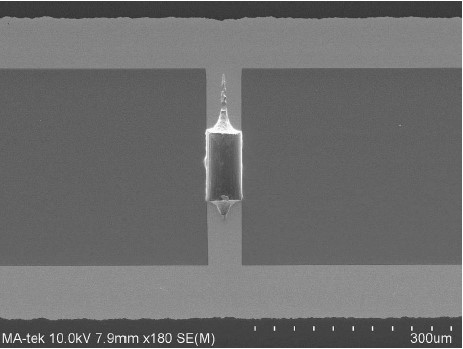
80um標準樣品金屬沉積厚度SEM圖(a)樣品表面
(b)孔洞中心
50um標準樣品電鍍結果之矽通導孔SEM圖
6.奈米銀金屬化製程導入矽導通孔之研究[學生郭珉豪]
因應市場對電子產品輕薄之需求,半導體產業不斷地快速發展。為解決目前二維製程微縮上所遇到的困難,讓摩爾定律(Moore’s
Law)能夠延續,應用矽導通孔(TSV)連接之三維積體電路(3D
IC)構裝技術成為產業積極發展的重要技術-其關鍵便在於矽導通孔製程。此矽導通孔的孔洞填充製程,屬具有優良導電特性與熱導率的銅電鍍製程為業界中最常使用的方式,但即使技術相對成熟,仍有許多製程困難處,像是電鍍品質相當依賴種子層(Seed
Layer)的沉積品質,以及須使用特殊設計之電鍍設備及鍍液,且電鍍時間往往相當長,因此如何突破目前業界中矽導通孔的發展瓶頸,開發出一低成本,且高品質的矽導通孔,為業界中的首要課題。
因此本研究提出將奈米化的銀漿導入矽導通孔,藉由銀金屬奈米化後之低熔點,且保有銀金屬導電性、熱傳導佳的性能,並配合基板結構設計之想法,以單個製程技術,同時完成孔洞金屬填充,與正背面所需的電路設計圖案,以提升此製程之價值與競爭性。
根據實驗結果,奈米銀成功利用實驗探討的近似最佳參數,獲得良好之矽導通孔品質,並且導入八吋矽晶圓,驗證其奈米銀金屬化於晶圓級矽導通孔的製程性。總結,本研究開發出一符合業界標準之金屬化製程技術,有效提供出一成本低廉、品質佳且具量產性之矽導通孔製程,為矽導通孔金屬化製程增加一新選擇。
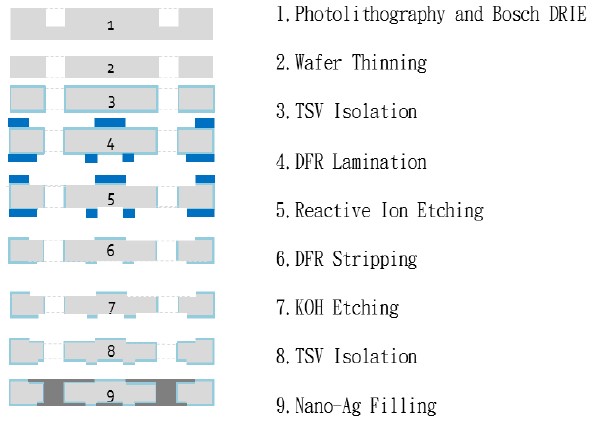
本研究所使用之奈米銀漿微觀圖
本研究矽導通孔晶圓製程流程
7.高精度數控拋光參數最佳化分析[學生黃士溥]
拋光是使工件產生平滑鏡面之超精密製造技術,直接或間接代表一個國家機械製造業水準,對於提高光機電產品的性能品質壽命與研發高科技產品等層面皆具有十分重要的作用。目前拋光技術對於球面鏡面加工已趨近成熟,雖然可以達到很高的表面形狀精度,但球面透鏡仍存在像差(Aberration)問題。為了改善此類狀況,球面透鏡常以多片鏡面組合,但卻因此而弱化成像對比度。相較之下,非球面鏡片局部曲率半徑會隨著徑向位置而改變,無法以固定曲率模具進行研磨拋光,只能利用電腦輔助進行數控拋光,但若能使用非球面透鏡取代球面透鏡,不但符合對於光學成像品質的要求,同時能大幅縮小光學系統之體積。
本研究針對數控拋光進行探討,針對不同拋光參數對於透鏡表面形貌之影響進行探討,並抑制拋光過程中所產生之中頻空間形貌頻率(Mid-spatial
frequency),進而提高整體拋光後表面品質;由實驗結果可知,數控拋光之拋光墊進給速率並非影響表面品質之重要參數,同時如果將拋光路徑旋轉並進行重複拋光,不但可以降低透鏡表面之峰谷值(Peak-to-valley)與方均根值,中頻空間形貌頻率誤差也可以被有效抑制。希望藉由本研究所歸納出數據,有效提升拋光後表面品質與重複拋光將表面粗糙數值收斂之效率,進而降低拋光過程所需時間及人力成本,因應國內精密拋光技術與機台發展。
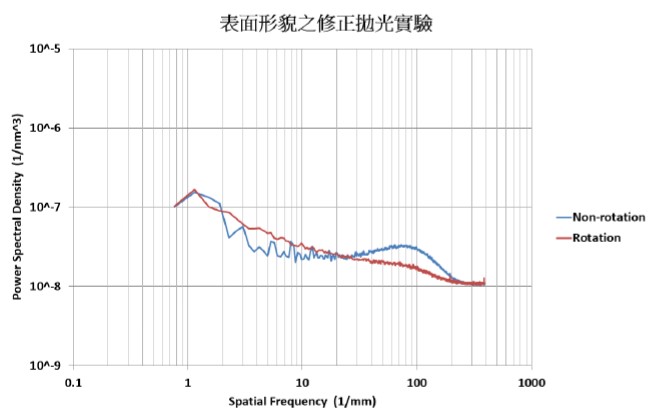
IRP1000超精拋光機
NPFLEX量測拋光墊轉速800rpm重複性拋光比較
NPFLEX量測表面貌修正拋光比較
|